Wind Overview
Wind Plant Description
The REMPD includes all components and associated materials required for utility-scale wind energy technologies up to the points of interconnection. For wind energy, this includes foundations or substructures, towers, nacelles, rotors, and balance-of-system components. It does not include transportation and capital equipment required to install, maintain, operate, or decommission wind power plants. Figure 2 illustrates the system components for wind energy in the REMPD, including wind turbines, onshore and offshore substations, and transmission cables.
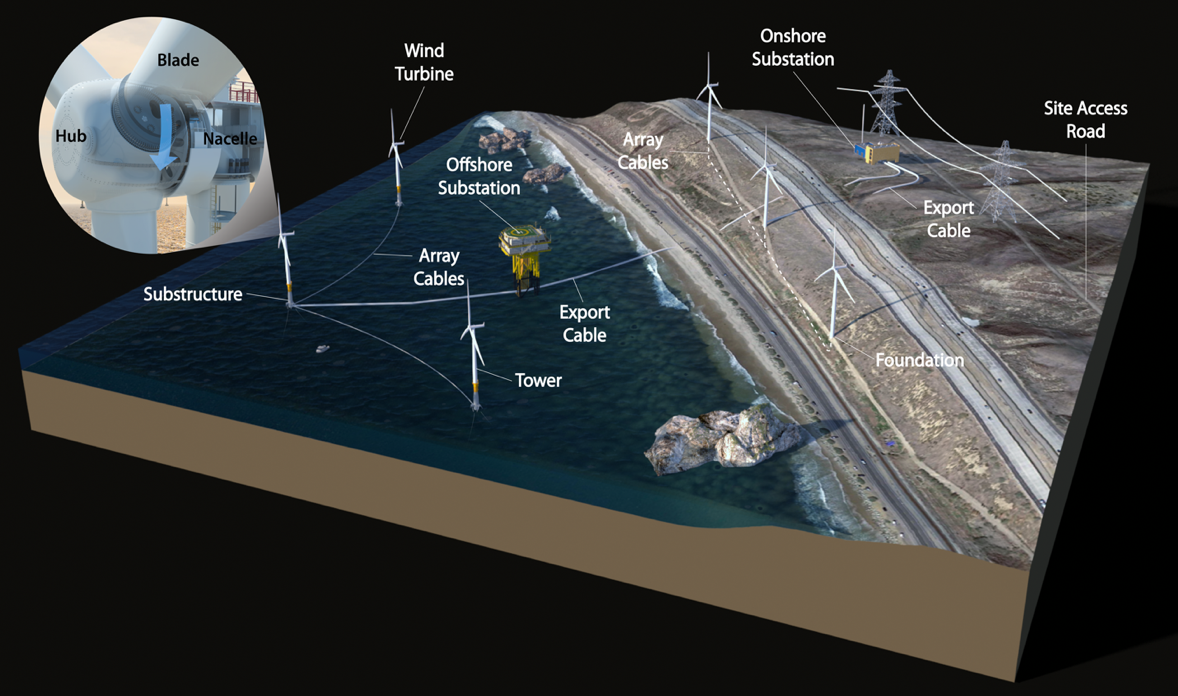
Utility-scale wind turbines included in the REMPD have a rated capacity of at least 1 MW and are installed within large wind plants that require additional infrastructure such as electrical cables and one or more substations. Land-based wind plants also require access roads. Roads are included because they are required throughout the operation of the wind plant; however, delivery and installation equipment, such as trucks, cranes, wrenches, and harnesses do not remain on-site at the wind plant and, therefore, are not included in the database. The REMPD assumes a typical plant size of 200 MW to estimate the amount of material required for land-based wind energy production (Wiser et al. [2021] indicates a wide range of U.S. land-based wind plant sizes, but a 200-MW wind plant size was selected as typical for recently installed land-based wind plants). Offshore wind plant sizes are typically larger than land-based wind plants; the REMPD assumes a typical offshore wind plant capacity of 1,000 MW, based on a range of publicly disclosed planned future offshore plant installations (Musial et al. [2022] indicates a wide range of offshore wind plant sizes, but a 1000-MW offshore wind plant size was selected as typical of new offshore wind plants). Offshore wind plants require different substructures than land-based wind turbine foundations; for example, steel monopiles have been used in many existing installations but other configurations are possible, including floating offshore wind in deep water. Table 3 lists the specific wind energy components and subassemblies that are included in the REMPD.
Table 3. REMPD Wind Energy Component and Subassembly Organizational Structure
Facility Type | Component | Subassembly (Technology Typea) | References for Material Quantities |
---|---|---|---|
Land-based wind | Array and export ables | Totalb | Proprietary data from original equipment manufacturers (OEMs) |
Foundation | Totalb | Proprietary data from OEMs; selected Vestas life cycle assessmentsc; Crawford (2009); Eberle et al. (2019); Schreiber, Marx, and Zapp (2019) | |
Roads | Totalb | Eberle et al. (2019) | |
Substation | Totalb | Proprietary data from OEMs; Alsaleh and Sattler (2019) | |
Turbine | Blade (conventional; segmented) | Proprietary data from OEMs; Eberle et al. (2023) | |
Hub | Proprietary data from OEMs; Crawford (2009) | ||
Nacelle (direct drive; gearbox) | Proprietary data from OEMs; Alsaleh and Sattler (2019); Martínez et al. (2009); Ozoemena, Cheung, and Hasan (2018); Rajaei and Tinjum (2013) | ||
Tower (conventional; sprial welded; hybrid) | Proprietary data from OEMs; Crawford (2009); Guezuraga, Zauner, and Pölz (2012) | ||
Offshore wind | Array and export cables | Array cable | Proprietary data from OEMs; ABB (2010); Arvesen et al. (2014); Ikhennicheu et al. (2020) |
Export cable | |||
Onshore cable | |||
Substation | Substation equipment | Proprietary data from OEMs; Arvesen et al. (2014) | |
Substation structure | |||
Substructure | Gravity base (fixed gravity base) | 4C Offshore (2022); Negro et al. (2017) | |
Jacket (fixed jacket) | |||
Monopile (fixed monopile) | |||
Piles (fixed jacket) | |||
Spar (floating) | |||
Suction buckets (fixed jacket) | |||
Transition piece (fixed monopile) | |||
Turbine | Blade (conventional; segmented) | Proprietary data from OEMs; Eberle et al. (2023) | |
Hub | Proprietary data from OEMs; Crawford (2009) | ||
Nacelle (direct drive; gearbox) | Proprietary data from OEMs | ||
Tower (conventional; sprial welded) | Proprietary data from OEMs; Crawford (2009); Guezuraga, Zauner, and Pölz (2012) |
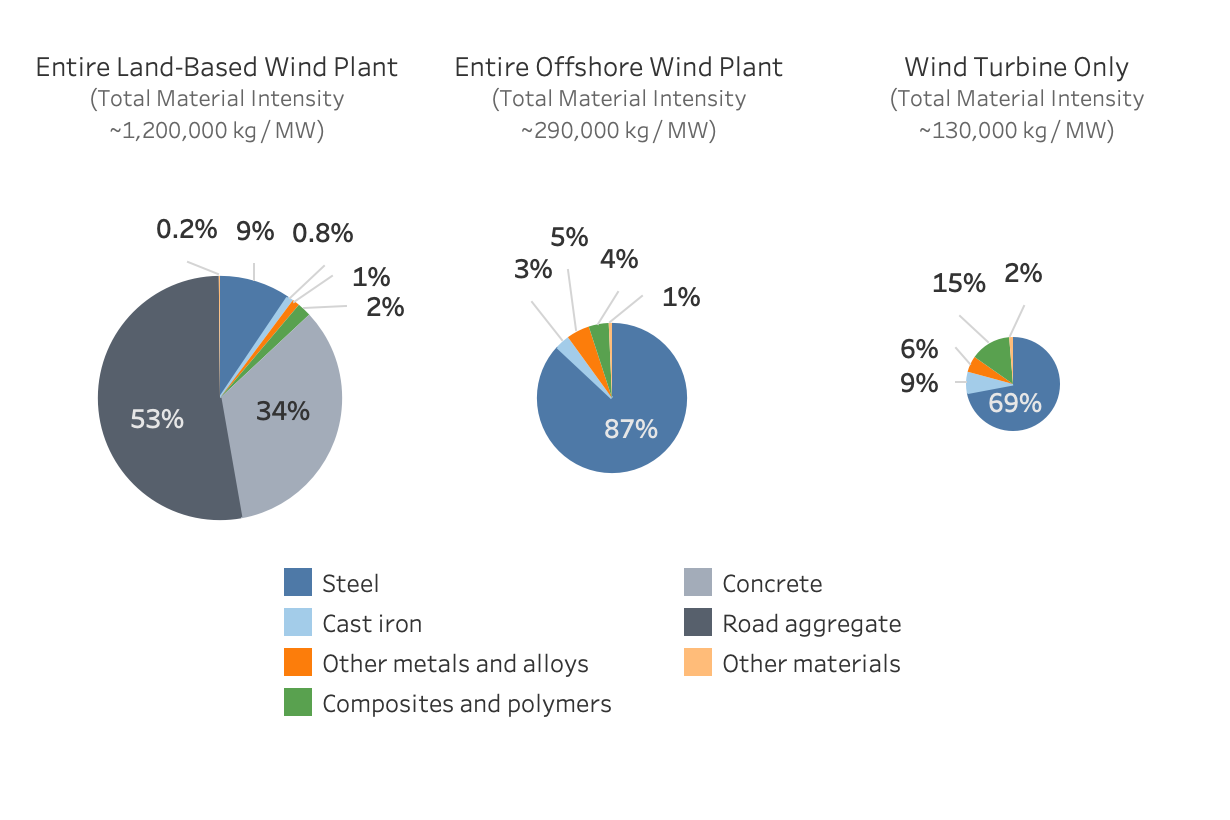
As reported in the REMPD, the main components of a utility-scale wind plant and typical materials used for each component include the following mass amounts for each subsystem:
- Blades (11,000–17,000 kg/MW per three blades).
- The blades primarily comprise composite materials that combine a polymer resin (e.g., epoxy; 2,000–5,000 kg/MW) with glass or carbon fibers (7,000–10,000 kg/MW) and a balsa wood or polymer foam core (1,200–1,300 kg/MW). There are typically three blades per wind turbine.
- Land-based: 13–18 metric tons per blade
- Offshore: 65–80 metric tons per blade
- Hub (4,300–13,000 kg/MW).
- The hub is made of cast iron (1,200–4,000 kg/MW) and is the structure that connects the blades to the nacelle and tower. Within the hub, the pitch system—which controls the orientation of the blades—predominantly comprises steel and other materials (3,100–9,000 kg/MW).
- Land-based: 18–44 metric tons per turbine
- Offshore: 64–179 metric tons per turbine
- Nacelle (18,000–36,000 kg/MW).
- The nacelle includes an enclosure that is typically made of fiberglass (300–3,500 kg/MW) over a steel frame (3,500–10,000 kg/MW) and cast-iron bedplate (3,000–5,000 kg/MW). Additional materials (6,800–17,500 kg/MW) used within the nacelle vary depending on the wind turbine configuration and differences between these configurations contribute to the wide range of nacelle masses. A geared turbine requires a gearbox, which contains alloy steel, brass or bronze, and cast iron. Most direct-drive generators use permanent magnets that contain rare-earth elements. The power transformer, which may be located in the nacelle or the tower, contains steel, electrical steel, and copper or aluminum.
- Land-based: 90–240 metric tons per turbine
- Offshore: 270–550 metric tons per turbine
- Tower (44,000–100,000 kg/MW).
- Most towers are constructed from tubular steel sections, although concrete or a combination of concrete and steel sections can also be used. Variation in the tower mass is primarily driven by different hub heights. Additional quantities of steel, copper, or aluminum are used in power cables and for personnel access equipment.
- Land-based: 310–340 metric tons per turbine
- Offshore: 670–710 metric tons per turbine
- Land-based wind turbine foundations are primarily comprised of concrete (390,000–405,000 kg/MW) with steel reinforcement (20,000–55,000 kg/MW).
- Land-based: 1,400–1,600 metric tons per turbine
- Offshore wind turbine substructures—including monopiles, jackets, and floating platforms—are typically made from steel plate.
- Offshore: 1,400–1,600 metric tons per turbine
- Electrical cables use aluminum or copper conductors and polymer insulating material (e.g., polyethylene). Submarine cables, which are used for offshore wind energy, require additional layers of lead or steel surrounding the conductive core(s). The total mass of cables varies widely depending on the distance from a wind plant to the electrical grid, the choice of material (aluminum is lighter than copper), the electrical capacity of the cable, and whether the cable is installed overhead, buried, or subsea.
- Land-based: 5–20 kg per meter of cable
- Offshore: 15–50 kg per meter of cable
- Substations require steel (200–1,300 kg/MW) and electrical steel (200–1,600 kg/MW) for power transformers and switchgear and copper (40–700 kg/MW) for wiring. Offshore substations require a steel support structure (7,000 kg/MW), whereas land-based substations use concrete foundations (200–3,600 kg/MW).
- Land-based: 400–1,800 metric tons per wind power plant
- Offshore: 7,000–8,000 metric tons per wind power plant
- Site access roads within a wind power plant are typically made from aggregate comprising crushed stones, gravel, or recycled concrete.
- Land-based: 100,000–120,000 metric tons per wind power plant
- Additional materials that are not specifically detailed here, but are available in further specified in the database, include protective coatings and paints that contain zinc (for corrosion resistance) or polymers such as epoxy. Electronic controls, sensors, lighting, and safety equipment contain various materials, notably semiconductors, which contain critical minerals.